I received a package of custom gaskets from
Cometic today. They are the largest gasket maker in the country, supplying both OEM and aftermarket manufacturers in a variety of industries. They were really easy to work with on getting several engine case and oil pan gaskets cut from their bonded rubber AFM material and on having MLS head gaskets made from a modified version of a ZX6R part.
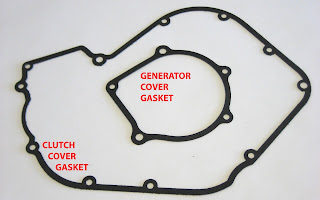

The clutch cover, generator cover, and oil pan gaskets are made from a chemically blown compounded nitrile synthetic rubber that is bonded to an aluminum core so they have a bit of strength and won't just rip like paper gaskets. The process was simple, I grabbed an outline of the appropriate surfaces from my CAD model of the engine, saved them as DXF files, and emailed them. A couple of weeks later- custom gaskets for a very reasonable cost. Cool stuff.
They can do the same for just about any sealing surface so if you have an old car, tractor, vintage bike, etc. that is hard to find gaskets for just give Mike Sauer at Cometic a call.
Head gaskets are not as simple a part as an engine cover gasket. They need to withstand high temperature and pressure loads cycling at a rate of over 200 times per second. For this reason I did not want to start from scratch and preferred to modify an existing Cometic part. They were able to modify one of their .018" thick Multi Layer Steel head gaskets to add material where needed and then trimmed the overall length to size.

Overall all the parts were within tolerances, so one more item completed on the road to a running engine.
That's all for now.
Chris